Manufacturing a Rotary Vane Pump for Seawater
Highlighted Skills
-
Manufacturing Skills: turning lathe, milling, laser cutting, riveting, CNC milling, water jet cutting, sand casting, and sheet metal bending
In Manufacturing Processes for Design & Production, I was tasked to use common engineering manufacturing skills on the shop floor to design and manufacture a rotary vane pump designed to move room temperature water up 1 foot.

Steel shaft turned on the lathe from a cylinder stock and then milled to create hex.

Shrink fitting of the shaft and rotor together. Rotor was heated; shaft was cooled. Assembly fixture on the bottom, labeled in orange.

Final rotor + shaft. Aluminum rotor was turned on lathe from a cylinder stock.

CNC mill the 4 slots for the vanes.
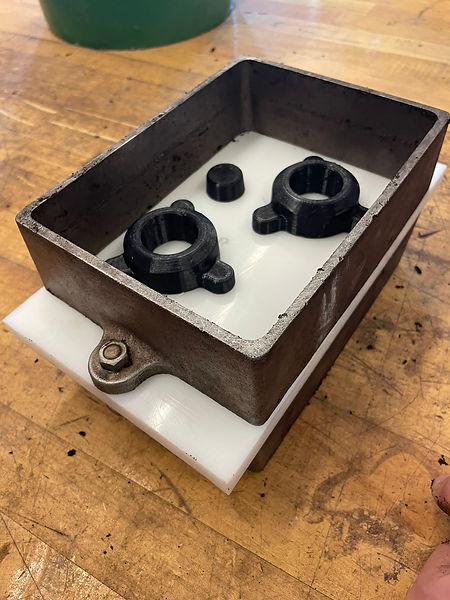
Sand casting tool for bearing housing.
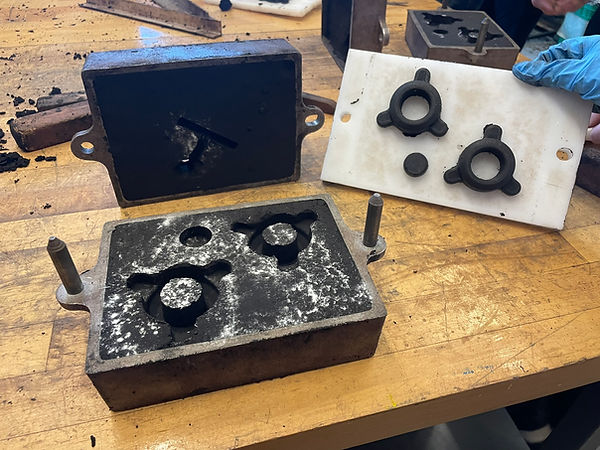
Sand is packed! Tool removed to reveal core.

More sand. Cope on top of the drag. Hole on top where the aluminum will pour into the sprue.
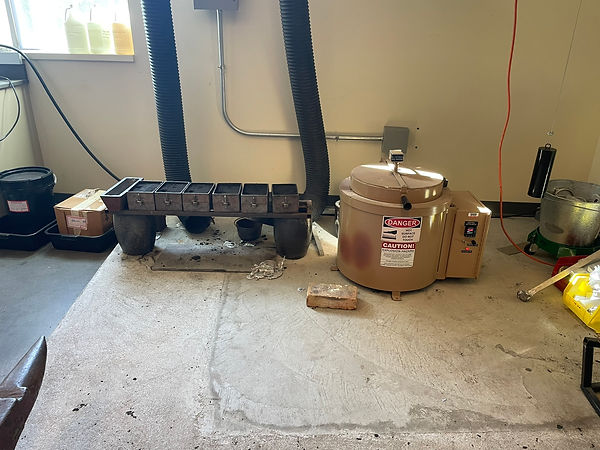
Where the magic happens, aka where the hot aluminum was poured into the mold.
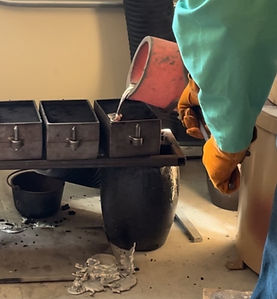
Pouring hot aluminum into the spruce.
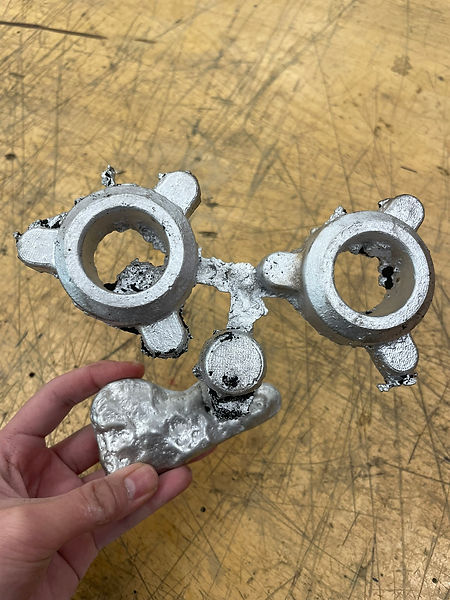
After the mold cooled down, I used tongs and dipped them into water to rinse off excess sand and further cool it down. After this, I separated the two parts with a band saw. The parts were then filed down and I used CNC to continue milling it to my desired dimensions.

Tapping holes to create threads in the acrylic front plate.
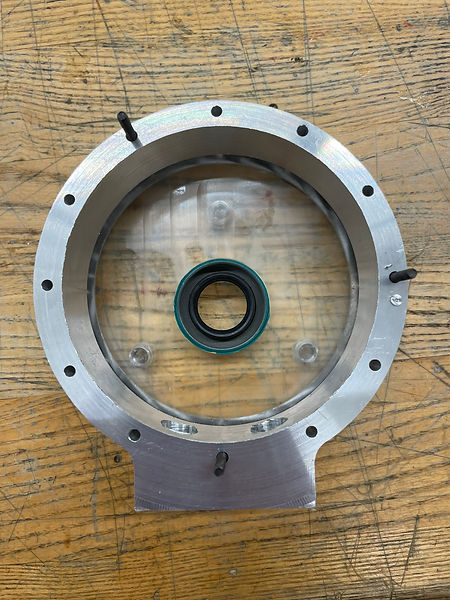
I press fitted the shaft seal into the acrylic front plate with a vice and some elbow grease.

The final pump. The stand was made out of a sheet of 5052 Aluminum bent to the desired shape and riveted together. The water jet cut front ring, front plate, laser cut gasket, housing, and back plate were assembled together with 12 low strength steel hex nuts. The vanes were milled from a long strip of Delrin.

Exploded view of water pump.